- How soon can Vibratec experts visit the offshore installation?
- How quickly can they propose solutions?
- Where the failures observed come from?
- How can these failures be prevented?
- What is the risk level of the issues? How soon the maintenance actions need to be done?
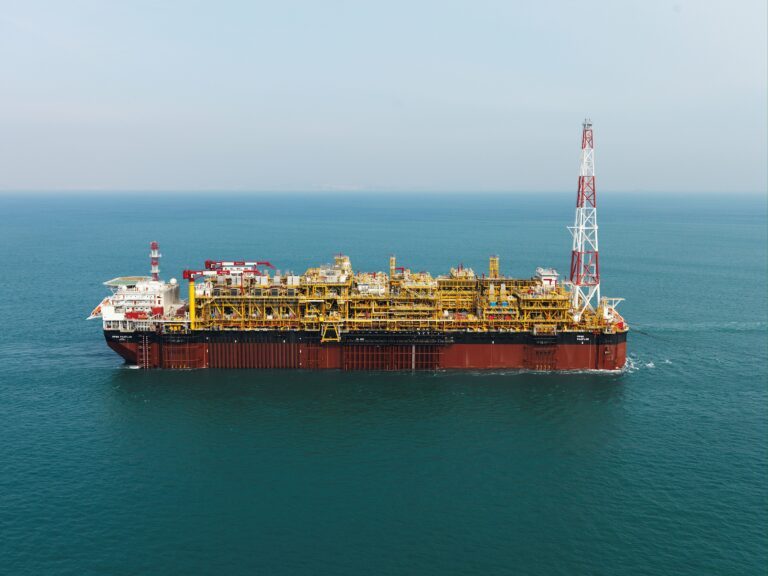
Crude oil line vibration diagnosis on a FPSO
Context & Issue
SBM Offshore was facing vibration issues and failures were observed on instruments and pipes on one of their FPSO.
These issues have critical consequences:
- Security of all the employees onboard the FPSO.
- Risk of production loss in case of imposed shut down of the installation.
The client objective was to clearly know the maintenance actions to be scheduled.
Main questions
Client benefits
01
Reactivity & autonomy
Two Vibratec experts were on-site, with all the specialized measurement equipment, less than 3 weeks after the client request for quotation and were autonomous for the diagnosis
02
Production respected
On-site diagnostic mission with no impact on the production
03
Risk assessment
The data collected were compared to the adapted specification to evaluate the risk of the issue and assess the maintenance emergency.
04
Integrable solution
All the solutions proposed are discussed and validated with the technical team of the client in order to ensure their integration on site
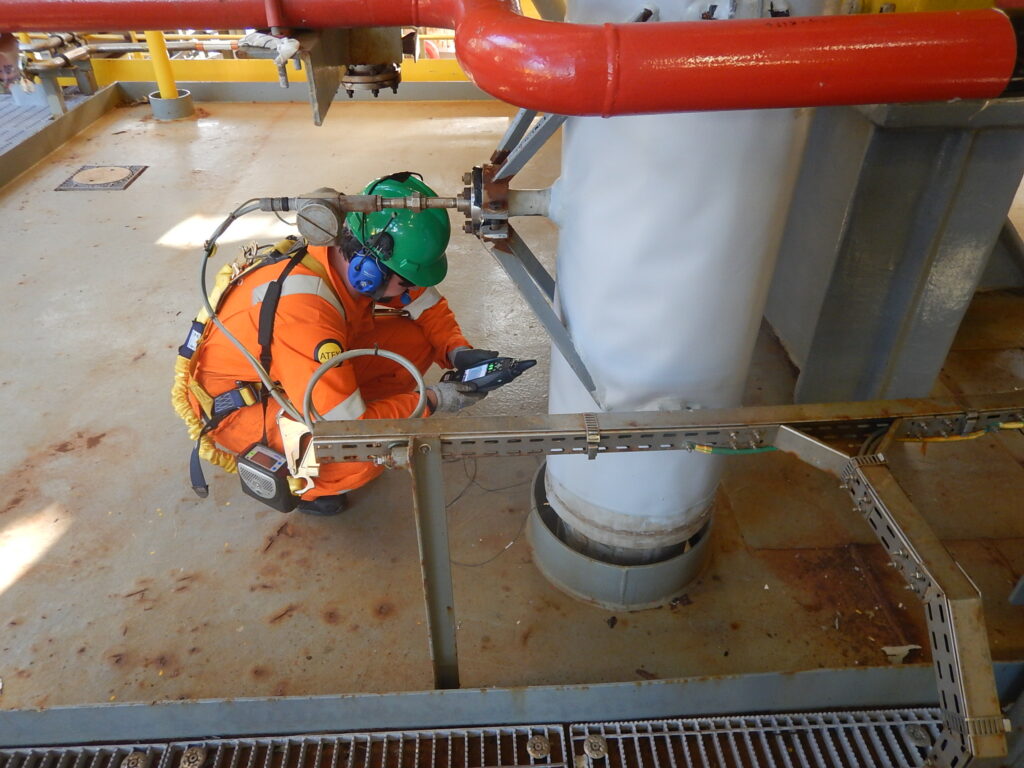
Challenges for Vibratec
01
Realized the adapted measurement on the right locations to understand the dynamic behavior
02
Proposed adapted solutions: issues correction and production site integration
03
Work with minimal impact on production
Piping vibration diagnosis
Instrumentation, Simulation, Analysis
Our expertise to serve your projects
Key Development Points
This type of problem often involves complex issues with many possible root causes. A methodical and complete approach was needed to understand all the physical phenomena and analyze the origin of the issues observed. To finally answer the client questions.
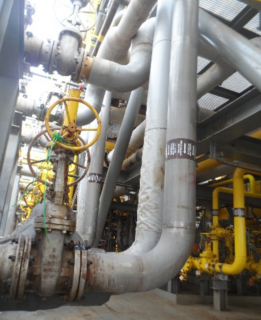
Measurement mesh
In order to visualize the piping deformation shapes when running, a meshing of the piping network was realized with 90 measurement points.
Tri-axis accelerometers are used for the measurement with a bandwidth [0 – 6400 Hz] and a frequency resolution 0.25 Hz.
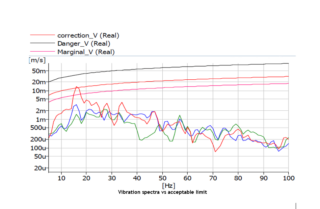
Vibration levels definition and specification comparison
The first measurements are realized at full load production condition.
The velocity levels are defined on the bandwidth [3 – 1000 Hz] for each 90 measurement points in mm/s RMS.
The levels are compared to the limits preconized on the Guidelines for the avoidance of vibration induced fatigue failure in process pipework – 2nd edition – 2008 from the Energy Institute specification.
This first analysis permitted to define the critical location on the line. It also permitted to determine a first risk of the vibration for the production: the installation was classified “correction needed” (orange curve hereafter) but not “danger” (red curve).
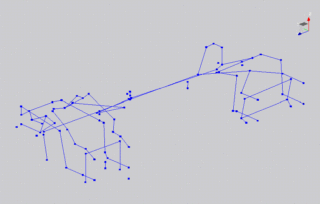
Operational Deformation Shapes
The Operational Deformation Shapes permit to focus on the point and location where the vibration level exceeds the limit and highlight the incriminated movements on the frequency range of interest.
These movements permit to determine the directions where the lines have a degree of freedom and estimate the localization which have not enough stiffness.
Some motions have been detected on the cooler and the heater between 7-10 Hz.
Experimental Modal Analysis
At this step it is necessary to ensure that these movement on some frequencies do not correspond to natural frequencies of the piping network.
The Experimental Modal Analysis permit to determine the natural frequencies and the associated deformation shapes. These measurements are realized without flow. The pipe network is excited thanks to an impact hammer.
The combination of the Operational Deformation Shapes and The Experimental Modal Analysis permit to understand the origin of the vibration and propose several mitigation actions.
The motions found on the cooler and the heater thanks to the Experimental Modal Analysis are very close to the motions found on the Operational Deformation Shapes. And the frequencies are also similar. Vibratec was able to conclude that the abnormal vibrations levels are due to the excitation of modes by a broadband excitation (a clear characteristic of Flow Induced Vibration phenomena).
Solutions
VIBRATEC proposed several solutions:
- Additional support or structure reinforcement
- Modification of support or fixation part
- Support repair
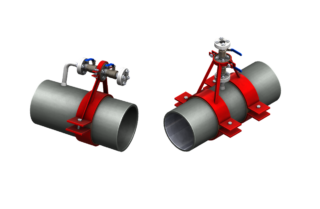
Want to know more?