It is possible to replace experimental qualification for certain products (carried out in a test cell or with a shaker) with numerical qualification (using a finite element model) in order to reduce the cost and duration of development cycles (or design correction cycles).
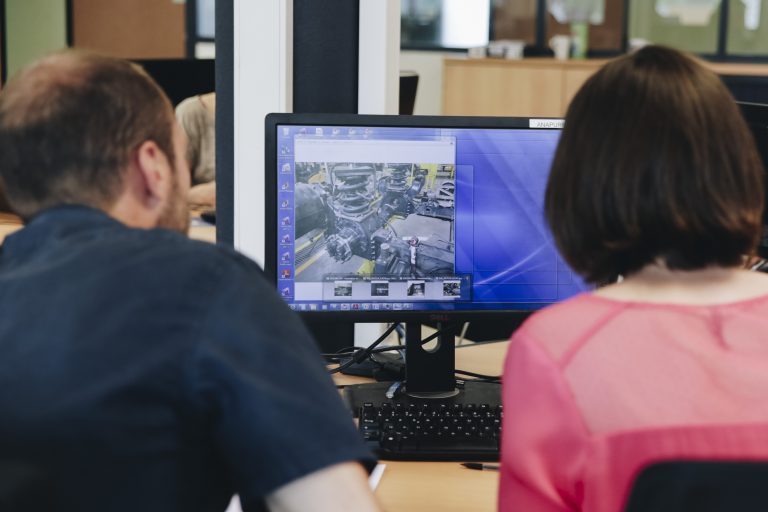
Test customization – Reliability and finite element modeling – Volvo Powertrain
Context & Issue
Challenges
01
Reduce development cycle time
02
Optimize costs
03
Increase project team responsiveness
Key Development Points
Identification and characterization of all loads (static, dynamic, temperature, etc.) using measurements
Static loads are forces that do not change over time. Measurements for this type of load can include the force applied, load position, angle of application and the duration of time the load is applied.
Dynamic loads are forces that change over time. Measurements for this type of load can include the force applied, the frequency of the load, load amplitude, the duration for which the load is applied and the characteristics of the load source.
Electric charges are charges that result from the flow of electric current in a given system. Measurements for this type of load can include electric voltage, electric current, current frequency, electric power and load source characteristics (e.g. type of power supply).
In general, to fully characterize loads, it is often necessary to measure several parameters simultaneously.
Representative finite element modeling of the part (business rules) and recalibration
Finite element modeling (FEM) is a numerical technique for representing the behavior of a part or system by subdividing it into a large number of finite elements. Each finite element is characterized by a set of material and geometric properties that determine its behavior. The finite element method is widely used in industry to simulate the behavior of mechanical, electromagnetic or thermal structures.
Response calculation and service life estimation
These methods make it possible to assess the effects of different operating scenarios on the residual life of the structure, and to plan inspections and repairs accordingly.
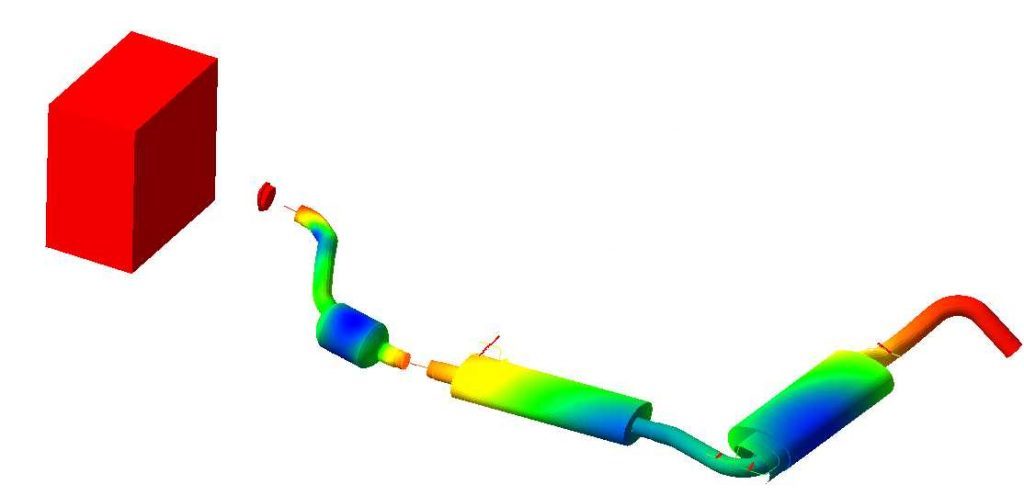
Results & Benefits
Product life cycle characterization
Service life can be influenced by a number of factors, such as product quality, design, materials used, operating conditions, environment, maintenance and servicing.
Design optimization to achieve desired service life
Optimizing a product’s design to achieve the desired service life requires an integrated approach that takes into account the various factors that influence product durability (choice of materials, design, reliability testing, scheduled maintenance).
Reduced costs and time for product development/modification
The use of numerical models can help reduce costs by identifying inefficiencies and proposing solutions to eliminate them.